Unleash Potential with Aluminum Casting Illinois: Our Promise
Wiki Article
The Ultimate Aluminum Casting Manual: Step-by-Step Instructions for Success

Safety And Security Safety Measures for Aluminum Casting
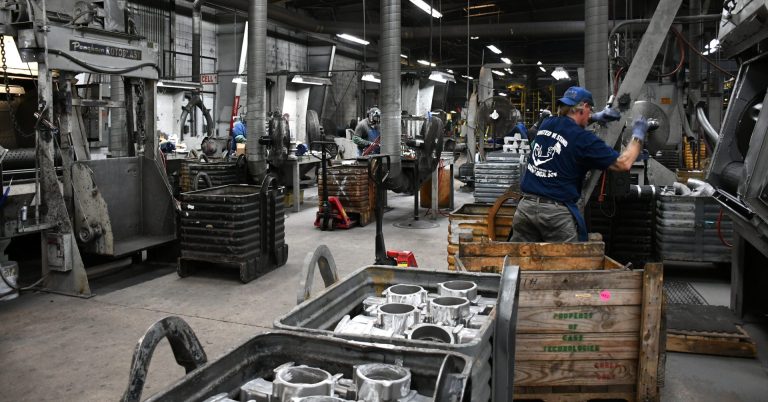
In addition, preserving a clean workspace devoid of mess can stop tripping threats and promote the activity of personnel throughout casting processes. aluminum casting illinois. Correct training in handling molten light weight aluminum and operating casting equipment is vital to reduce the threat of injuries and mishaps. Regular tools upkeep and evaluation ought to be performed to determine and fix any possible safety risks without delay
Establishing Your Aluminum Casting Office
Establishing a safe and effective work area for aluminum casting is essential for making certain smooth operations and minimizing potential hazards. Prior to establishing up your office, guarantee that it is well-ventilated to avoid the build-up of damaging fumes produced throughout the casting process. Organize your devices and tools in a rational manner, keeping them within easy reach yet likewise maintaining clear pathways for motion around the work space. It is important to have a designated location for each and every stage of the casting process, such as pattern production, mold preparation, and steel pouring, to simplify operations and avoid cross-contamination. In addition, make certain that your work area is equipped with fire extinguishers and emergency situation safety devices, and that all workers are learnt proper security procedures. Use heat-resistant materials for job surface areas and floor covering to stop damage and accidents due to high temperature levels. By thoroughly intending and setting up your light weight aluminum casting workspace, you can create an effective atmosphere that focuses on security and effectiveness.Choosing the Right Light Weight Aluminum Alloy
To make certain optimal casting causes your well-organized and safety-focused work space, choosing the suitable aluminum alloy is paramount. Different aluminum alloys supply diverse characteristics such as toughness, longevity, warmth resistance, and machinability. The choice of alloy depends on the particular needs of your casting project.One typically used aluminum alloy for spreading is A356. This alloy shows outstanding fluidness, making it optimal for detailed spreadings with thin wall surfaces. A356 also has great deterioration resistance and mechanical residential or commercial properties, making it appropriate for a vast array of applications.
If greater stamina is called for, 7075 aluminum alloy is a prominent option. Known for its high strength-to-weight ratio, 7075 is usually made use of in applications where stamina is critical, such as aerospace components.
For tasks that entail high-temperature environments, 319 aluminum alloy is a good alternative due to its superior thermal conductivity and resistance to thermal fracturing.
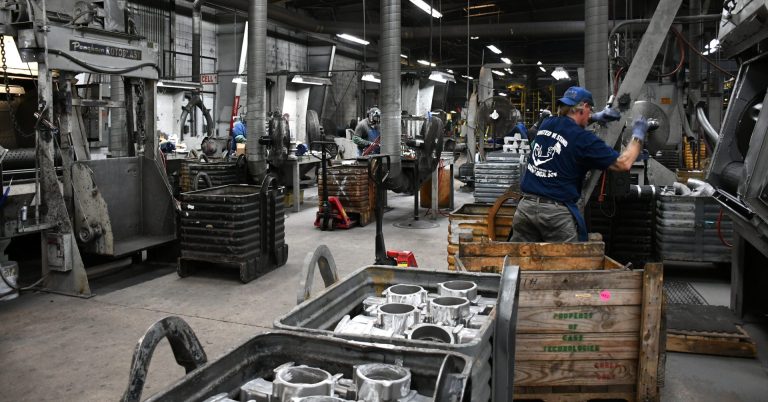
Step-by-Step Light Weight Aluminum Spreading Process
Beginning the aluminum spreading process includes precise prep work and adherence to an exact collection of actions to guarantee the manufacturing of top quality castings. The primary step is pattern development, where a reproduction of the end product is made from steel, timber, or plastic. This pattern is after that used to develop the mold and mildew, which can be constructed from products like sand or plaster. When the mold and mildew is prepared, it is time to melt the light weight aluminum in a heater at temperature levels surpassing 1200 ° F.After getting to the wanted temperature, the liquified light weight aluminum is poured right into the mold tooth cavity. This step needs caution and precision to prevent issues in the last spreading. The light weight aluminum is left to cool down and strengthen inside the mold before it is gotten rid of for ending up. Post-processing strategies such as grinding, fining sand, and warm treatment may be employed to accomplish the preferred shape, Go Here surface area finish, and mechanical buildings.
Throughout the entire procedure, mindful monitoring and high quality control steps ought to be applied to guarantee the last light weight aluminum spreading satisfies the called for requirements and criteria.
Tips for Refining Your Spreading Method
In refining your light weight aluminum spreading strategy, thorough attention to detail and adherence to precise steps are vital to making sure the manufacturing of high-grade spreadings. One important idea for refining your spreading strategy is to thoroughly prepare the mold and mildew and ensure it is tidy and properly covered with a release representative to help in the very easy removal of the spreading. Additionally, preserving the light weight aluminum at the proper temperature throughout the spreading process is necessary for attaining optimum flow and reducing the danger of flaws. Another idea is to put the liquified light weight aluminum gradually and steadily into the mold and mildew to avoid air entrapment and guarantee a smooth fill. It is additionally crucial to permit sufficient time for the aluminum to strengthen entirely before removing the spreading from the mold and mildew. Inspecting the casting for any type of flaws and making essential adjustments to the procedure will aid you enhance and excellent your light weight aluminum spreading technique over time.Conclusion
To conclude, following appropriate safety and security precautions, setting up a suitable work area, choosing the appropriate aluminum alloy, and diligently adhering to the step-by-step casting procedure are vital for successful aluminum spreading. By paying focus to these vital factors and including ideas to improve your technique, you can accomplish excellent lead to your aluminum casting tasks.From safety preventative measures to improving casting strategies, this handbook offers as a beacon of expertise for those venturing into the world of light weight aluminum spreading.
Starting the light weight aluminum spreading procedure entails careful preparation and adherence to a specific series of steps to ensure the production of high-grade spreadings.In refining your light weight aluminum spreading Home Page technique, meticulous attention to detail and adherence to accurate actions are critical to ensuring the manufacturing of top quality spreadings. One vital pointer for developing your spreading strategy is to meticulously prepare the mold and ensure it is clean and his explanation properly coated with a release representative to assist in the very easy removal of the spreading. Inspecting the spreading for any imperfections and making essential adjustments to the procedure will aid you enhance and ideal your aluminum spreading method over time.
Report this wiki page